The power of concrete
VELDHOVEN - blog #3 Tuesday 8 September 2020
In this third blog entry, Gerard talks about the power of concrete.
“There is always something with concrete.”
These words are printed as the title of an article I see on my smartphone. Initially, it evokes defensive emotions in me, but I quickly realise that these words are simply a cry for attention for one of the most versatile construction materials in the world.
Luckily, there is always something with concrete. Not for the first time, I say:
“Concrete is alive and adds character to a project.”
Constructive forces
The misconception that people see concrete as an artificial, dead material is really a thing of the past. The constructive forces that this, potentially also colourful, material is able to absorb in conjunction with its durability, begin to develop as soon as the natural raw materials are mixed together and, upon the addition of water, start to take the shape of the casing. A concrete object is born and there is a transformation from a liquid mixture to a solid shape, known as the 'hydration process'. The reaction of water with cement forms a glue that mixes around the aggregates. Over time, it develops into an increasingly hardened mass.
In the first hours of this process, heat is released as part of the reaction. Covering concrete elements after pouring them is good practice: not only moisture but also heat is retained in the concrete element. If you remove the cover from the element the next morning, you can feel the warmth. Hold your hand above a concrete surface – you can feel it.
The colour of concrete
Throughout the process you also see the colour of the concrete surface change. This is a particular aspect that plays tricks on us, as concrete technologists, when we have to deliver smooth, coloured, visible concrete.
“Yes – Great! Exactly the colour I imagined.”
These words were enthusiastically spoken during a session of creating several concrete samples. Unfortunately, I have to temper such enthusiasm somewhat: the colour of the fresh and still wet concrete will change during the hydration process and will become a different colour to the wet mixture - shame. In order to achieve a smoothly coloured concrete skin in the desired colour, you have to consciously use a different composition. This is often a complicated process, as you have to take into account the shape of the elements to be made. A partially thicker concrete element will release heat differently than a thinner element. The time an element spends in its mould also affects the colour effect. As builders of precast concrete, we regularly look up – while driving past beautiful residential towers – to see whether there is a ‘postage stamp’ element in the facade. These could be elements that were poured on a Friday afternoon, for example, and therefore not removed from the mould the next day according to a fixed pattern, but after the weekend on the Monday morning. These are all factors that have an effect on the result. As long as the ‘concrete skin’ is smooth, you will see this more clearly.
The discolouration effect is present in every composition, but choices can be made to limit the effect. Smooth white is a good example: it goes through the same hydration process but there is hardly any discernible difference.
The smooth concrete skin is sensitive, so we often show the process it has gone through. A different effect is created from the same concrete: whatever you put into the concrete can be made visible through blasting – washing - polishing. The natural aggregate material maintains its own colour and sometimes also structure. The aggregate particles used are, of course, bonded together by the (coloured) cement paste and it undergoes the discolouration described. However, your experience is that you can see much more of the natural and colourfast aggregate as visible element.
Look-alike
No two concrete mixtures are the same, and each mixture has its own process. No single concrete element will be exactly the same as another, it is impossible. There is also only one unique Gerard Brood in the world. Perhaps there is a look-alike somewhere, or a like-named person, but it goes no further than that, thank goodness.
It is possible to produce a certain predetermined concrete colour. As such, there are the so-called Dutch CUR recommended 100 grey scales. However, these apply only to smooth, grey concrete products. As soon as we move on to coloured concrete, we have to act differently. We start by making reference samples, in order to agree what the possibilities are. For example, we need to switch from the recommended class B1 or B2 to class B9, specifically intended for a non-uniform grey coloured concrete surface, according to the same CUR 100.
The result
If someone asks me to make dark red/brown or uniform charcoal coloured concrete for a 100-metre tower, well, anything is possible, but within Byldis this triggers alarm bells. You have to be aware of what will happen in the long-term. The concrete is alive, and the binding process ensures that the pores will close and that during this process – sooner or later – lime particles will be deposited on the surface of the concrete. This chalky residue on the surface of the concrete is caused by calcium hydroxide seeping out of the pore water. Upon reaction with carbon dioxide in the air, the (white) calcium carbonate is deposited. We make precast concrete puzzle pieces every day using raw materials that can react slightly differently every day. A fantastic game that keeps us busy on a daily basis. Every day we see the birth of a new piece of the puzzle that will be released from its casing the following day and that we will watch grow into an essential component of a construction. Everything in a tight production schedule, whereby the process must be given the chance to develop optimally within the predetermined conditions. In some ways, the contradictory nature of being patient goes hand in hand with this fast, precast concrete mindset. Waiting is often seen as wasting time, but it is actually essential in achieving the desired result. It is like baking cookies: you would never take them out of the oven early in order to save time because you know they would not taste good.
In the car, on the way home, I see residential towers we made in the past and I think:
“Yes – indeed, there is always something with concrete!”
Written by: Gerard Brood, Senior Quality Officer at Byldis Prefab
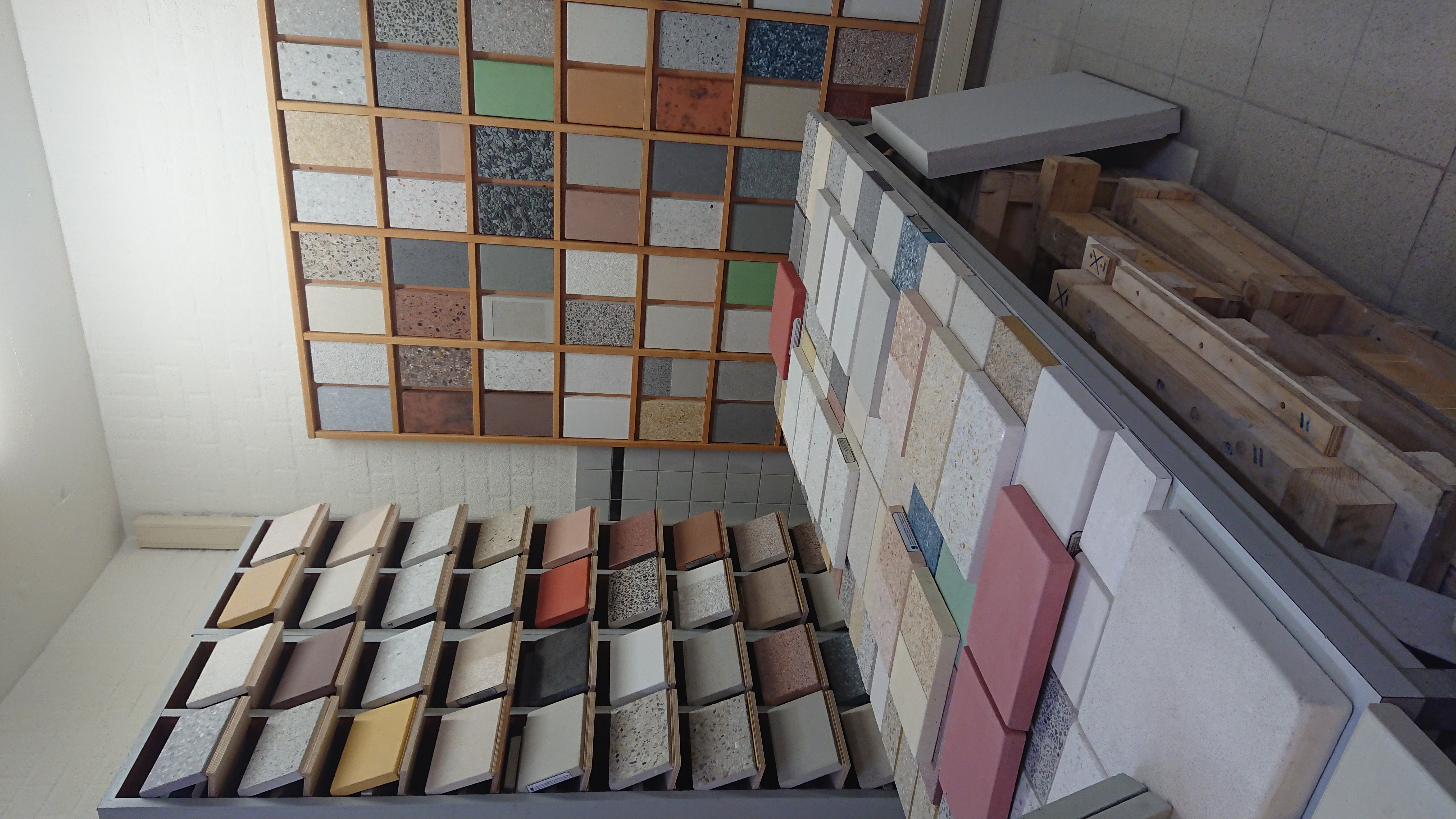
The various examples of kinds and colours of concrete available!
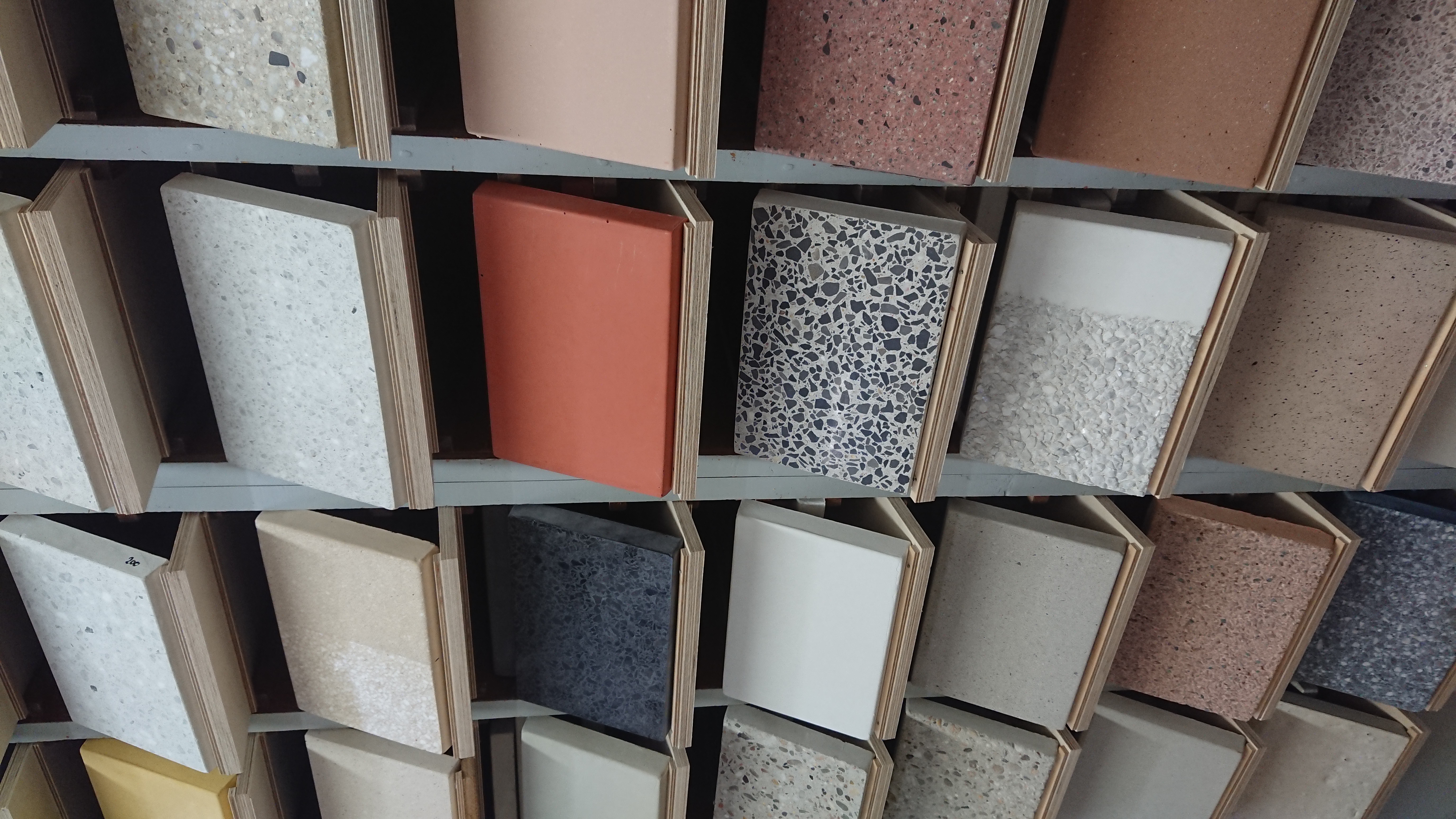
All these 'tiles' are in Gerard’s workplace.
But wait... there's more!
In "Concrete chunks", Gerard Brood talks about his work as Senior Quality Officer and Concrete Technologist at Byldis. As well as a passion for his work, he also loves describing his observations. Want to read all the blogs? Go to: all concrete chunks.